OUR PRINCIPAL SCIENTIST DIVES INTO THE IMPORTANCE OF UNDERSTANDING PFAS COMPOUNDS AND THE REMEDIATION OPTIONS AVAILABLE
BY: BRAD LEWIS
Perfluoroalkyl and polyfluoroalkyl substances (PFAS) are part of a broad chemical group that were first developed in the 1940s. Since then, there have been nearly 5,000 different PFAS compounds that have found their way into commercial use. Some of these compounds are now being phased out due to toxicity concerns, however new fluorinated compounds like Gen X and ADONA are being developed to replace them.
PFAS are well known for their unique chemical properties that repel oil and water and resist temperature, chemicals, and fire. They also have electrical insulating properties. These are the attributes that make PFAS attractive and are why they are found in many durable industrial and everyday products and materials like non-stick surfaces, firefighting foam as a flame retardant, stain resistant materials, water repellent coatings and plating demisters to name a few.
WHY ARE PFAS AN ISSUE?
PFAS chemicals are everywhere and they don’t break down. This is why PFAS chemicals are known as “forever chemicals” because they never go away.
The chemistry is complex because PFAS are not one chemical compound, they are a class of chemical compounds that share the common carbon-fluorine bond however they vary widely by their size, structure, toxicity, and mobility in the environment.
The carbon to fluorine bond is one of the strongest bonds in organic chemistry, making PFAS compounds particularly resistant to degradation. Since they do not break down and they were used in lots of materials, they are being found everywhere in the environment. States like Michigan have made the effort to test public and private potable water supplies for PFAS and have found them to be more widespread than previously thought.
HOW DO PFAS CYCLE THROUGH THE ENVIRONMENT?
A lot has yet to be learned about even the more commonly encountered of the PFAS compounds. Despite their size, these compounds have relatively high water solubility and are surprisingly mobile in the environment, especially in groundwater.
PFAS are resistant to treatment and degradation, and typically go through water and wastewater treatment plants untouched and end up in discharges to surface water and to the land. Since they persist and go largely untreated, they often cycle through the environment and create widespread impact as shown on the graphic from the Michigan Department of Environmental Quality.
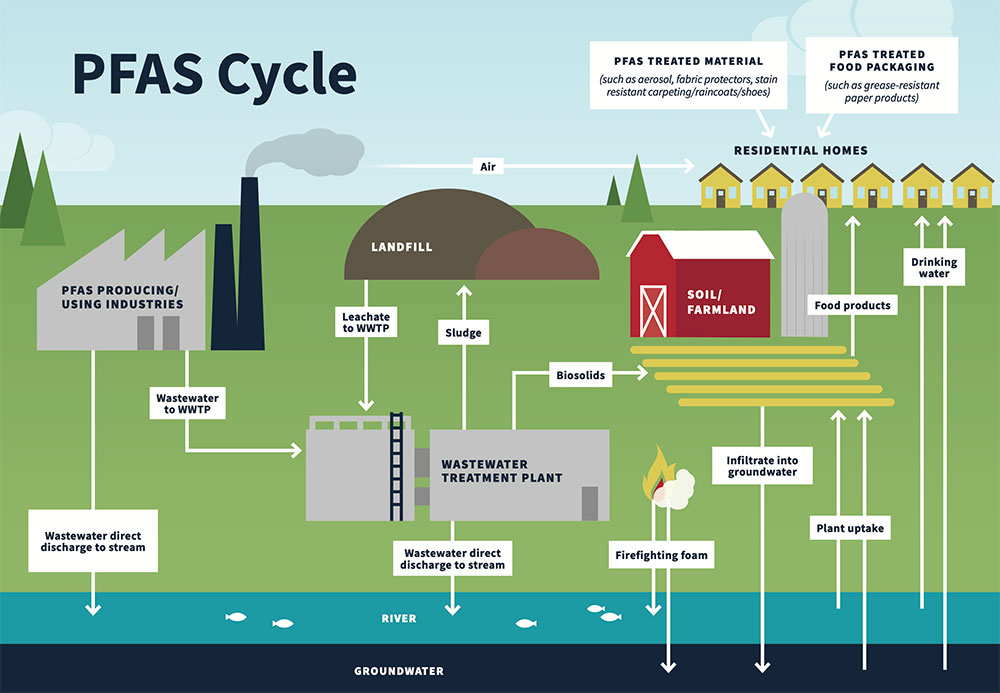
The concern for human health is due to the PFAS compounds tendency to have long residency time in the human body, which is known as bioaccumulation. This combined with their largely unknown human health toxicity, means that we do not currently understand how big of a health concern this is at the moment. The lack of toxicity studies along with the fact that it is being found everywhere, poses a significant concern for regulators in charge of human health and the environment.
Currently, regulators are trying to establish criteria for PFAS compounds while at the same time scientist are trying to establish the different compound’s toxicities. The situation is very fluid and there will be a lot of changes to the science and regulations.
HOW DO YOU KNOW IF THERE MAY BE PFAS CONTAMINATION?
PFAS were used in a variety of industries. There may be PFAS contamination in the groundwater or soil at manufacturing sites of the following products:
- Textiles and leather with coatings to repeal water, oil and stains
- Paper products with surface coatings to repel grease and moisture
- Metal plating to prevent corrosion, suppress fume and reduce wear
- Wire manufacturing through the coating and insultation processes
- Industrial surfactants with plastics, mold release coatings and flame retardants
- Photolithography for anti-reflective coatings and wetting agents
- Along with ski waxes, cookware, fabric softeners, pesticides, windshield wipers, medical products, personal care products and dental floss
Or businesses that use Class B firefighting foams, such as:
- Airports
- Military bases
To date, the majority of the PFAS cleanup sites have been at large chemical manufacturing plants and military properties where aqueous firefighting foams (AFFF) have been used.
HOW ARE PFAS REMEDIATED?
It’s very difficult to remediate PFAS. PFAS compounds are very resistant to biological, chemical and heat degradation; therefore, many of the remediation techniques that are used for petroleum and chlorinated solvent sites are largely ineffective on PFAS. Since they cannot be easily degraded, they need to be removed.
Most remediation technologies to date have focused on pumping water from the ground and treating it through either reverse osmosis systems or filtration (carbon or ionic) media. However, this simply concentrates PFAS onto a different media that now needs disposal. Soil impacts are typically excavated and disposed of at off-site disposal facilities. As this issue comes to light, more disposal facilities may reject these waste streams.
Currently, there is a lot of on-going research on innovative methods to either remove or stabilize PFAS in the ground to decrease its mobility or to destroy it with thermal or chemical methods. These technologies are a long way from being proven and time tested. Like everything with PFAS this an ever-changing playing field.
HOW ARE PFAS REGULATED?
The United States Environmental Protection Agency (US EPA) has yet to define PFAS as a hazardous substance; therefore, it is not yet subject to all of the CERCLA regulations. This lack of hazardous substance designation also means that there is somewhat of a grey area for whether PFAS should be considered a Recognized Environmental Condition (REC) during real estate due diligence process. Buyers should be cautious when doing Phase I Environmental Site Assessments (ESAs) and should consider State designations and the most recent US EPA updates.
PFAS aren’t widely regulated yet in the United States on a Federal level. Some states like Michigan, Wisconsin and New Jersey have gotten out in front of the US EPA and have established state regulatory limits for a small number of the more commonly used compounds. At this moment, PFAS regulation is primarily state specific, so it’s important know what a state’s status is on PFAS regulations.
In late 2019, the US EPA established a PFAS Action Plan to study and formulate regulations ranging from adding PFAS to Toxic Release Inventory (TRI) toxic chemical list to recommendations for addressing contaminated groundwater and preliminary drinking water regulations for Perfluorooctanoic acid (PFOA) and Perfluorooctanesulfonic acid (PFOS). A more thorough examination of the Federal and State regulations can be found on the Interstates Technology Regulatory Counsel (ITRC) Basis of Regulations website.
HOW CAN YOU TEST FOR PFAS IN DRINKING WATER?
For now, the US EPA has established a drinking water Health Advisory Limit for just two out of nearly 5,000 PFAS compounds but is deep into a long regulatory process of establishing enforceable limits. Some states have expanded on this and are regulating additional PFAS compounds.
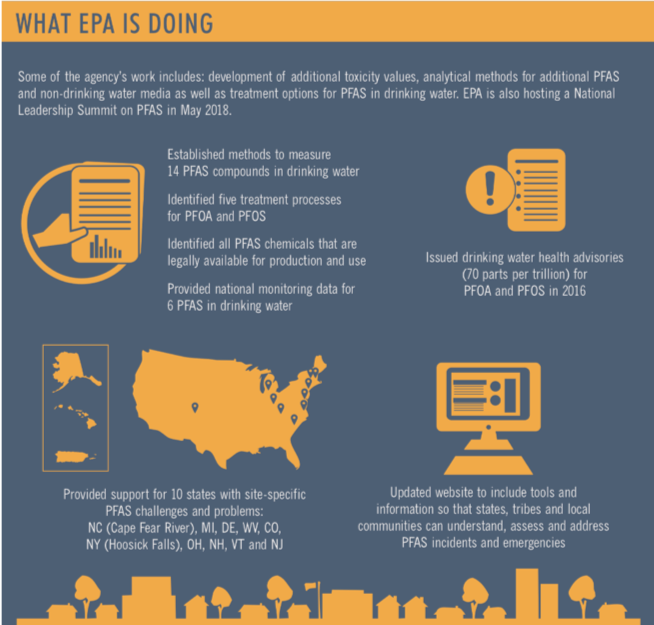
Testing for PFAS is a complicated proposition because:
- The testing methods are still evolving (currently focused mainly on drinking water)
- Laboratories are still investing in equipment and training to perform the testing
- The detection limits established so far are very low (70 parts in a trillion parts or ppt)
- These compounds can be found in a lot of background sources in both the field sampling equipment and the laboratory equipment (high potential for false positives)
- Tests currently only look for a small number of the more common compounds
The most important thing to establish if a regulator asks you to sample for PFAS is which compounds are required and at what detection levels. Then discuss with your laboratory if they can detect those same compounds at those same low levels. It is very important to vet your lab’s experience with analyzing for this emerging contaminant. You will also want to be sure that your samplers have taken precautions to limit the potential for contamination of the samples from everyday products (plastics, coatings, sunscreens, stain proof fabrics).
WHAT IS MICHIGAN DOING ABOUT PFAS?
Michigan is one of the pioneering states in the race to test drinking water supplies for PFAS. They sampled over a thousand community water supply wells and non-community water supply wells and found that the drinking water had low levels of PFAS chemicals. They’ve also tested wastewater from treatment plants and streams.
As already mentioned, other states that are working hard to develop the regulations are Wisconsin and Minnesota.
WHAT CAN WE EXPECT GOING FORWARD?
In a lot of ways PFAS are the perfect storm of an emerging contaminant. They have widespread use, they are not easily treated, they persist in the environment, they bioaccumulate and they are thought to have health effects down in the low parts per trillion (ppt) levels.
The science and the regulations are evolving as we speak, and much will change in the next couple of years. If you are faced with the proposition of sampling your site for PFAS, take a deep breath and do not be in a rush to charge forward. Take time to understand what you are being asked to do and what are the applicable standards to which you will be held. What applies today may be very different from what applies tomorrow.
Contact us to learn more about environmental contaminants like PFAS.
Brad Lewis, CHMM, Principal Scientist at EnviroForensics
Brad Lewis is a detailed-oriented and collaborative leader with 30+ years of environmental consulting experience that covers a variety of projects ranging from due diligence, environmental compliance, landfill, Brownfields, underground storage tank, and chlorinated hydrocarbon investigations and cleanups. As Principal Scientist, he oversees investigations and cleanups. He helps project teams set the technical and regulatory strategies that will meet their client’s goals. Lewis has implemented many innovative site investigation strategies including the use of down-hole sensing equipment, mobile laboratory, and an immunoassay to characterize sites.
He has consulted on many high-profile projects dealing with petroleum hydrocarbons, polychlorinated biphenyls, hexavalent chromium, chlorinated solvents, bedrock impacts, vapor intrusion investigations, and vapor mitigation.