It can feel like their whole world has been turned upside down when our clients receive the news that they have an environmental contamination issue on their property that could take hundreds of thousands, or millions, of dollars to clean up. Adding to this sense of panic is the knowledge that active remediation activities can be intrusive, time-consuming, and potentially disrupt business operations. The risk of losing loyal customers during forced down-time can keep anyone up at night. That’s why EnviroForensics goes to great lengths to work with drycleaner owners to make sure we’re doing our job while also allowing them to do theirs.
Recently, we began the process of remediating a Site in Indiana where the best remedial technology necessitated work inside the drycleaner building. The owners needed to keep the business running uninterrupted, and we needed to work with them to make that happen. We put our heads together and came up with a schedule and approach to install our remedial components while minimizing the impact on the drycleaner’s ability to conduct normal business.
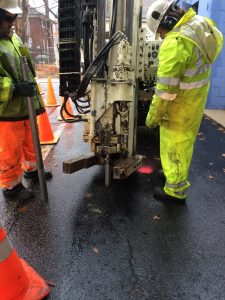
The first task was the installation process involved installing ozone sparge points into the groundwater beneath the Site building. Ozone sparge technology is able to oxidize contaminants in groundwater through the injection of ozone through subsurface injection points. For this phase, we devised a way to stay out of our clients way altogether by drilling angled sparge points from outside of the building to reach the contaminants beneath the building. This innovative approach allowed for normal cleaning operations to continue inside the building during the drilling activities.
The second step of the installation process was a little bit trickier since it necessitated the installation of soil vapor extraction (SVE) wells and above ground piping inside the building. We were able to schedule this portion of the work during February, which has historically been one of the slower times of year for our clients. For two weeks, dry cleaning and laundry operations were conducted as normal from 8am to 2pm before the building shifted into remediation mode. The front desk and pick-up/drop-off operations continued as usual while our experienced install team went to work installing the SVE system from 2pm until 10pm each night. Pulling those second shift hours paid dividends for our dry cleaning partner by allowing them to keep the doors open and meet the cleaning needs of their customers. Now, while the public gets their dry cleaning finished on time, our remediation system is keeping a low profile, cleaning up soil and groundwater impacts.
Staying open is a big deal. For some business owners, it’s absolutely necessary to keep their heads above water. For others, it’s just a powerful statement to their loyal customers that they can continue to serve them in spite of their commitment to improving environmental conditions at their site. Keeping our client’s best interests in mind is a vital part of our job, and we demonstrate this on each and every project through team work and innovation to develop new solutions to old problems. We work hard behind closed doors so yours can stay open.
This poster is prominently displayed outside the actual drycleaner. It was put up to help maintain transparency between the business and its loyal customers as well as establish the drycleaner owners as stewards for the environment.